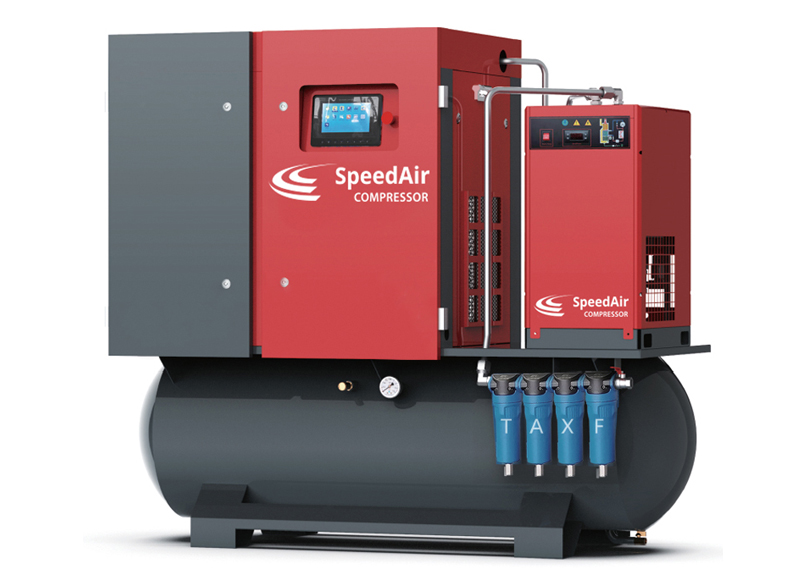
LASER CUTTING SCREW COMPRESORS 16 BAR
Selecting a Screw Compressor for Laser Cutting
When choosing a screw compressor compatible with laser cutting machines, certain features that affect the cutting quality, efficiency and long-term costs of the system should be taken into consideration.
Features That a Screw Compressor Should Have:
High Pressure and Flow Capacity:
Laser cutting machines generally require a pressure between 8-16 bar and sufficient air flow (flow).
The air flow should be calculated according to the capacity of the machine (for example, between 200-2000 L/min).
Constant Air Flow:
It is important that the pressure remains constant during cutting. The compressor should provide an uninterrupted and fluctuating air flow.
Air Quality:
The air used for laser cutting should be dry and oil-free.
A compressor equipped with an air dryer and filtration systems should be preferred. Oil Mist Separator and Chemical Air Dryer Must Be Used.
Particle filter: Cleans dust and particles.
Oil filter: Removes oil mist.
Air dryer: Prevents corrosion by removing moisture.
Energy Efficiency:
Variable speed (VSD) compressors optimize energy consumption according to air demand.
They should be equipped with an efficient motor for low energy costs.
Noise Level:
Models with low noise levels (generally <70 dB) should be preferred to improve working conditions in industrial areas.
Durability and Reliability:
A robust structure that can withstand long-term cutting operations.
Regular maintenance requirements should be low.
Additional Components:
Air Tank: Provides uninterrupted air supply and pressure balancing.
Easy-to-Install Systems: Compact design for quick commissioning and connection.